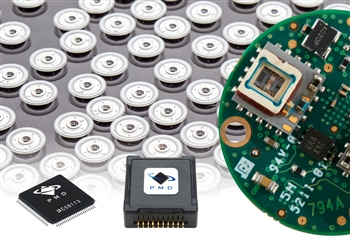
Designing with the End Goal in Mind
Selecting the right components and sub-systems when designing modern machines and technical equipment requires the consideration of many factors; some more obvious than others. Gerard Bush of INMOCO offers some insight into the process.
The Iterative Journey to Concept Development
Engineering designers usually start a project knowing what they want their machine or equipment to achieve; naturally to working backwards from there to get an idea for an initial concept design. It is then a matter of going back and forth, considering different issues and details until a concrete idea is formed. From here the designer may bring in the expertise of a colleague or two, build a prototype – real or virtual – or have a chat with potential end users and develop a strategy for the next stage of the project.
Selecting Components: More Than Just Specs
However the project evolves, there will come a point where components have to be selected. The designer may start by thinking: ‘we need a motor’, then they will have to consider the technical details of the motor (size, power, speed, dynamic performance, life expectancy, cost, etc). This may lead them towards selection of a particular motor or, perhaps more likely, to a short list of candidate motors.
They may then think: ‘we also need a controller for the motor, plus some sensors for feedback, plus other environmental sensors, plus a gearbox, plus an on/off switch, plus a safety cut-out, plus a housing, etc, etc.’
Why Compatibility Matters in System Design
One issue the designer will need to address is the compatibility of the various components – will they work together well, complementing rather than compromising each other. This can be quite a subtle thing to grasp, but to illustrate it: would you pair a miniature motor with an outsized controller, a precision encoder with a basic sensor, a top of the range gearbox with a cheap-and-cheerful coupling?
Balancing Performance, Cost, and Reliability
Identifying appropriate components requires mental reference to the ‘big picture’ – the overall concept of the project. Are you trying to produce a cost-conscious machine, or one that is ultra precise; or one where reliability is king because in-field repairs are going to be almost impossibly difficult; or one with a long working life in a harsh operating environment; or one that may be required to sit dormant for a long time but which can be trusted to ‘fire-up’ when finally required to do so?
Expertise in Motion Control Integration
At this stage many designers will appreciate the help of a specialist, another engineer, one with years of experience and expertise in a particular field, such as motion control. A critically important part of their skill is knowing which products will work well together and which combinations should be avoided. To illustrate this, we can look at some case studies, focussing on embedded, miniature precision motion control.
Case Study: Spin it to Win it – Centrifuge Design
Spin it to win it
Laboratory centrifuges used in life sciences have to operate at very high rotational speeds. They may also need positioning capabilities so samples align with access covers. They will require a motor, controller, and feedback device, each of which must be compatible with the others and with the duty requirements.
The motor will need to run at say 20,000 rpm; it will also need to be small, quiet, reliable and clean. A brushless DC motor would fulfil these requirements.
An encoder will probably be the best type of feedback device: perhaps surprisingly a low-cost quadrature encoder may be appropriate. These produce a constant rotational position signal as the motor spins, but can be prone to loss of accuracy at high speed. However, they are suitable for centrifuge applications, if the motor controller is able to produce a real-time indexing signal, which will enable automatic on-the-fly position correction. Thus a relatively low cost solution has been identified that is simple and uses well proven component technologies so is likely to be reliable.
Case Study: Two-Axis Motion in Microscopy
Two-axis motion
Microscope x‐y stages need fast, smooth, and accurate motion, but like centrifuges cost effectiveness is a must. The solution will require two independent servo motors, multi‐axis point‐to-point motion capability and an IC or Printed Circuit Board based controller. One solution would be an all‐in‐one motion board design incorporating say a Magellan motion control IC and the two motors. The axes will need mechanical actuators, probably of the leadscrew or linear motor type.
Significantly four encoders are also required: a rotary one on each motor, and a linear one on each axis. The rotary encoders are used to stabilise the motion, while the linear one provide position information. This dual loop automatically corrects for mechanical errors from backlash and leadscrew or table assembly non‐linearities. The Performance Motion Devices single axis MC58113 supports this dual encoder input and in addition is able to provide very tightly coupled contouring functions when combined with other MC58113 ICs.
Case Study: Microelectronic Wire-Bonding Precision
Microelectronic wire-bonding
As semiconductors become ever-more compact, wire bonding machines need to become better, faster, smaller more accurate and lower cost. This means the motion control systems must offer constantly improving high speed positioning, excellent repeatability and high resolution. Naturally, the motion system requirements include very small motors and actuators capable of producing smooth movements and accurate positioning, coupled with a controller that meets the demanding speed and precision requirements of the application.
The motion feedback encoders need to perform in a high electromagnetic interference (EMI) environment with good thermal stability, long cable flex life and high reliability. Miniature encoders such as the Mercury II line from Celera Motion (previously known as MicroE) are cost effective options for such duties, while the inclusion of a programmable input filter will help to eliminate the effects of high frequency noise in the encoders.
Case Study: Rotary Axis Control in Robotics
Robots turn for the better
A larger scale industrial application that Celera encoders have been used on is a precision rotary axis control for multiple sequential robot arm joints. Key additional requirements included minimal movement at start-up to report absolute position, and minimal signal cabling to keep the overall arm size as small as possible.
The solution chosen involved developing custom-sized PCB-based encoder modules fitted to a rotary disk containing an optical grating. The disk has a reference track in which each index mark is uniquely spaced so that with only a small movement at start-up, multiple index marks can be detected allowing the absolute position to be determined. The system can then be further improved by using two encoders in parallel and comparing the outputs.
Conclusion: Compatibility as a Design Philosophy
It is important that components used in the same system are compatible with one another. Determining the compatibility is not an exact science. It relies on both common sense and experience. Companies, like INMOCO have this expertise and have a product portfolio with a high degree of compatibility between its different ranges. INMOCO engineers are able to think about component compatibility automatically and can fast track your needs towards optimum design solutions.