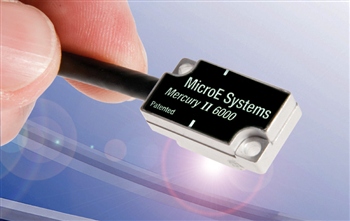
Inmoco’s new Mercury II™ 6000 series of encoders from MicroE Systems’ sets new benchmarks for sensor size, resolution and accuracy. The sensor is only 8.2mm high, weights just 3 grams and provides output resolution as precise as 1.2 nanometers. These features, plus the flexibility for use with tape, linear glass, or rotary scales with stick-on index and limits, make the Mercury II 6000 series ideal for use in demanding applications such as microscopy, life sciences, automated optical inspection, fibre optics manufacturing, instrumentation, laser processing, metrology, and many more.
The Mercury II™ 6000 series can reduce the size and cost of many motion systems; at the same time improving system performance in high speed, high resolution applications. It opens up a new range of capabilities in compact, high-end motion control stages and positioners, through its combination of accurate nanometer-level positioning, compact system design, and unprecedented affordability for the performance level provided.
Designed for both linear and rotary applications, Mercury II 6000’s exceptional cyclical error (short-travel accuracy) of ±20 nanometers delivers the precise nano-positioning feedback and smooth velocity control of fine pitch encoders costing 2-3 times more. Key to attaining this performance is low jitter – essential for nanometer applications – which is achieved by a combination of optical design, signal processing electronics and a user-programmable low pass output filter. In addition, low heat generation at the sensor minimises errors and distortions due to thermal effects, resulting in high signal stability and up to ±1.2nm of repeatability.
Mercury II 6000 is adaptable to the widest range of application requirements: output resolution is user programmable, ranging from 5µm to 1.2nm, linear, and high speed applications are supported by the fastest A-quad-B output in the 20µm encoder class, providing up to 1m/s at 20nm resolution. In addition, optional serial word output increases encoder speed capability to 10m/s at 1.2nm resolution.
The simplicity of the Mercury II 6000 design enables fast setup to be achieved with minimal skill. Key to this operation is Mercury II’s optical system, which features the broadest alignment tolerances of any 20µm-pitch encoder – particularly in the Theta Z axis. Rotational tolerance about this axis is ±2° – fully 300% better than the next best competitive encoder – and ride height tolerance is ±0.15mm.
Also optimising system set-up time, adhesive-mount PurePrecision™ tape scales provide accuracy, robustness, and rapid installation. The MicroE Systems’ PurePrecision™ system allows the installer to cut any required length from a reel of tape scale. The adhesive backing on the tape and a unique application tool do the rest, making installation fast and accurate. Linear glass scales satisfy applications requiring long-range accuracy up to ±1µm. Index and limit marks can be built-in or applied as stick-on markers.
In order to satisfy the widest range of user requirements, three versions of the Mercury II 6000 series have been introduced, all with low power consumption: 50mA @ 5VDC at the sensor – a fraction of other encoders in this resolution class. Version 1 is supplied with digital outputs for A-quad-B, index, dual limits and alarm. Version 2 is rated to 10 8 torr vacuum, and bake out at 150°C for 48 hours. Version 3 is the Mercury II 6800Si, with high speed serial output in SPI format for servo control at speeds up to 10m/s with 1.2nm resolution.