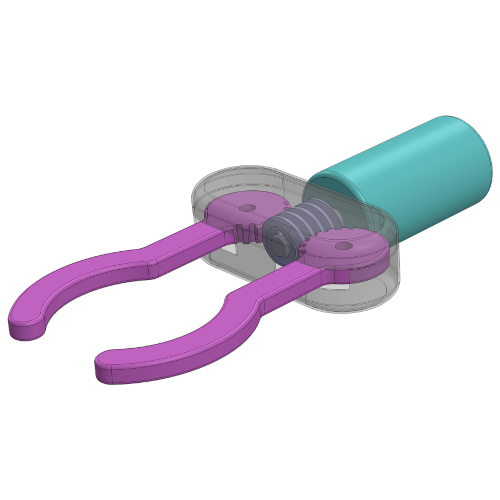
Robot end effectors are required in environments from the deep sea to the surgical theatre. While position control is necessary, the application must also integrate force sensing to ensure sensitive handling. Increasingly, robot end effectors also need to be actuated with remote and even virtual operation. To achieve accurate and repeatable control, careful specification of the motion system is essential.
Gerard Bush of motion specialist INMOCO explains the motion control techniques behind robot end effectors.
Motion Systems for Robot End Effectors
The basis that gives life to a robot end effector, such as a gripper, is its motion system. To position the end effector, and then enable it to grip with the precise amount of force, the required techniques depend on factors including the desired accuracy and repeatability of control. Focusing mainly on position control at outset, the most common configuration of servo actuator in an end effector application uses a rotary motor coupled with a lead screw, converting the motor’s rotation into linear motion.
The choice over rotary motor is wide, and dependent on requirements, a DC brush or brushless, servo, or a step motor can be used. While the rotary motor and lead screw actuator system is used for applications where optimum positioning accuracy is not a requirement, it’s still suitable to cover a wide range of industrial uses. Moreover, adding an external force sensor also enables this system to achieve precise force control.
As an alternative motion system for applications that demand high reliability and fast response time, direct drive linear brushless DC motors generate motion with no gears or lead screws needed. Direct drive motors also have very high acceleration, and though torque output is moderate if standard magnets are used, this capability can be upgraded. Force can also be controlled without the need for a separate sensor, as external torque presented to the actuator will be ‘felt’ directly by the servo system. Another category of direct drive linear actuators is the linear DC motor. These can be configured with a moving magnetic rod, delivering modest torque and speed, yet the simplicity of design achieves reliability and low cost. Alternatively, a voice coil actuator arrangement shares a modest torque output but provides an extremely fast response time.
Techniques for Force Control
As well as position, force has to be controlled for optimum end effector coordination, particularly in the case of grippers. Once contact is made, the gripper should apply a consistent force on the object, large enough to ensure a secure hold but without damaging it. The gripper is controlled by a servo PID (proportional integral derivative) feedback control loop that continuously monitors the motor torque command. This is then converted to end effector applied torque via the motors’ torque output-to-current ratio.
As the gripper begins to make contact, this is sensed in the servo loop, and the motor command torque increases to follow the commanded trajectory. Once the desired grip force has been achieved, dependent on the compliance of the object, the command to the motion profile is halted accordingly. Another approach is to use a current output limit in the servo loop, so even if the PID tries to follow the trajectory, the force it applies will be no greater than the desired force threshold. The current loop is critical because accurate force control is predicated on the ability to output a precise current through the motor coils. Also, an assumption for force control is a need for relatively low friction between the actuator and the object being sensed.
Alternatively, for applications involving a rotary-to-linear actuator combined with a strain gauge to measure force, a common approach is to add an outer loop controller that commands either the velocity or torque loop used to drive the motor. Here, the force command is combined with the force sensor value and passed through a PID filter. This outer loop then sends a corrective signal to a downstream velocity loop. The motor is commanded, forward or backwards, on a continual basis to precisely maintain the desired force.
Remote and Virtual Motion Control
To sense the presence and type of objects within the end effector’s motion range, this can involve remote teleoperation with force feedback, as used in robotic surgery or applications such as dangerous materials handling. In these cases, a human operator manipulates a mechanical replica that remotely controls the robot, while receiving force feedback information from the remotely operated device.
If the remote-controlled robot encounters an obstacle, such as a wall, as the operator continues to push their remote actuator forward, the force output of the remote mechanism’s motor will increase rapidly. In turn, this force will be fed back to the operator, who could even be enabled to feel subtle gradations of force, depending on the physical nature of the object encountered. Combined with a force multiplication (or reduction) system, this enhances operator control, required, for example, to enable a syringe needle to carefully penetrate an object as small as a biological cell.
Motion systems can also exist in a virtual environment. In an aeroplane simulator, for example, the virtual pilot handles a yoke, designed to present the same feedback that a pilot in the real world would experience. Even in these virtual environments, where a computer simulates feedback, the basis is the same as the remote system; interaction with a servo-based system can sense the operator’s movements and impart a force that the operator can feel. Even a simple, single-axis motor, controlled with a PID control loop, can be used to achieve a virtual system.
Optimising End Effector Specification
Requiring control over position and force, specifying a motion coordination system for end effectors can be achieved with a wide range of actuation and feedback devices. To achieve accuracy and repeatability, working with a motion control specialist like Performance Motion Devices (PMD), with an extensive portfolio of end effector projects, gives OEM engineers confidence in design. At INMOCO, our engineers interface between the OEM and PMD to ensure an exacting specification and a smooth development process.
About Performance Motion Devices
Performance Motion Devices, Inc. (PMD) is a world leader in motion control technology for life sciences, robotics, and industrial automation. PMD’s full line of advanced motion control solutions provide single and multi-axis motion control for Brushless DC, DC Brush, and step motors. Our motion control ICs, modules, and boards give our customers a wide range of motion control solutions while providing unparalleled packaging flexibility. OEMs and engineering teams worldwide rely on our components to build automation and machinery with the highest performance, the highest reliability, and the lowest cost.