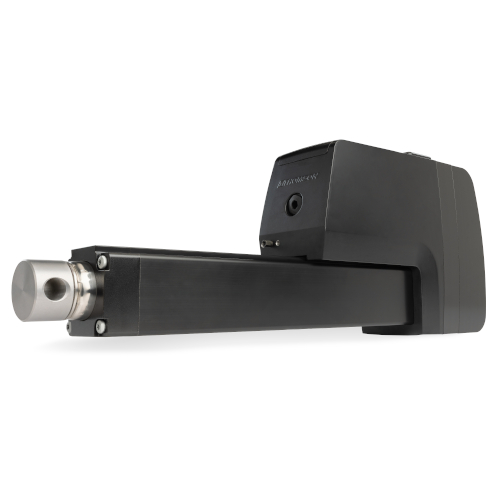
Overview of the Electrak XD Actuator
A new electric actuator can take on pushing and pulling tasks that previously only hydraulic devices could achieve. The Thomson Electrak XD actuator can handle dynamic loads up to 25,000N, and the actuator offers a large stroke up to 1.2m. Heavy-duty design and construction give the device long life, and the actuator can run for up to 275,000 cycles. Thomson products are distributed in the UK by INMOCO, and INMOCO’s engineering team can engage with OEMs to ensure smooth design integration.
Applications Across Industries
The Electrak XD actuator has been designed for applications in material handling, such as autonomous guided vehicles (AGVs) and logistics trains, as well as transit mobility, including work platforms, wheelchair lifts, and ramps. In agriculture and forestry, the actuators can be integrated on harvesters and automated pickers. The actuators can also be installed in factory automation for any machine that needs to pull and push loads, as well as wider general uses, such as forklift trucks.
Performance and Environmental Benefits
As well as being able to handle high dynamic loads, the new heavy-duty electric actuator can support static loads up to 32,000N. Generating speeds up to 75mm/s, the Electrak XD can also operate at 100% duty cycle. Designed for operation in arduous environments, the actuator has IP66 protection under dynamic operation and is tested to 500 hours of salt-spray resistance. The device operates with an input voltage and current draw of 24Vdc/30A or 48Vdc/15A.
Customisation and Control Features
To aid conversion from hydraulic to electric, the actuator includes control features such as an internal load-holding brake and a manual override. An optional manual release can also provide load release without power. Onboard features also enable monitoring of the actuator’s exact speed, position, and force.
Converting to electric-powered actuators reduces the size, complexity, and long-term cost of the system by eliminating a large number of components and consumables typically required with a hydraulic system. This also increases design process flexibility.
The sealed Electrak XD actuator is also maintenance-free. Removing the need for hydraulic oil, as well as lubricant, saves time and cost in management and is significantly cleaner. While critical for hygienic applications, cleaner operation decreases maintenance requirements in all settings. The device can also reduce energy costs and is a more environmentally friendly solution.
Thomson is providing five models of the Electrak XD, each with different stroke lengths and load handling capabilities. The actuators can also be customised to suit, such as providing different rod end adaptors. Various voltages, speed and force ratings, or stroke lengths can also be supplied, along with even higher IP ratings and surface treatment. Customisation can include the integration of various electrical connections, sensors and switches, as well as software and controls.
Onboard electronics enable control, including low-level switching, and communications take place via CANopen or SAE J1939.
INMOCO Support and Distribution
INMOCO can work with OEM engineering teams and Thomson’s customisation capabilities to achieve the required functionality and integration options, and the UK distributor can also provide a variety of associated motion control products.