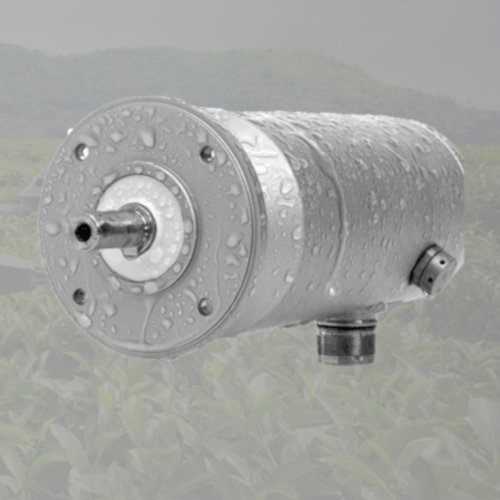
Robotics and automation have the potential to transform farming to a more productive and efficient model. Servo motors will be vital to power this equipment, providing high levels of precision control. However, these motors will face the rigours of the farm environment, including adverse weather, corrosive substances, as well as the challenge of a regular washdown. To reliably power smart agricultural machinery, servo motors must be built to last.
Gerard Bush, engineer at motion specialist INMOCO, explains.
According to recent reports, revenue in the agriculture service robotics market in the UK is projected to total £29.25m this year (1). Moreover, growth is expected at a rate of 15%, resulting in a market volume of £59m by 2029 (2). This kind of tech has an increasing range of uses in farming, from selective harvesting, to crop care and weeding, as well as identification of the highest yielding varieties in a crop.
Technology developments towards Smart Farming have the potential to make agricultural production more efficient, productive, and sustainable. However, robots operating in fields across Britain is not yet a common sight. Farmers need to rely on tried-and tested technology that works in all weathers, at all times of year. Technology developers for the agricultural market not only have to demonstrate the effectiveness of their designs, but they must also convince the market of their reliability and long service life.
Demands on servo motors
Essential to drive smart farming equipment such as agricultural robots is the electric motor. Servo motors are the primary choice as they achieve the high resolution and precise control required by a robot to make exacting moves, often at high speed or with rapid changes in position. This kind of control is required to help an agribot maintain balance on uneven ground or enable a harvesting robot to pick fruit.
Depending on the scale of the application, a variety of power ranges might be required for the servo system, along with the necessary torque and speed for a range of farming tasks. High torque density is often required, both to minimise the footprint of the application, as well as maintain low weight, crucial to optimise efficiency for mobile applications like robots.
While precise control can already be achieved by the servo motors and drives used in an industrial setting, the environmental demands placed on them in a farm setting could be much tougher. Farm equipment is continually exposed to harsh conditions including dirt, dust, moisture, mud, fertilizers, and insecticides, as well as adverse weather.
Protection from the elements
Liquid and solid ingress must be prevented, so as Kollmorgen, which designs servo systems for rugged environments, offers protection up to IP69K. This not only prevents ingress when used in the field but also means the motor can withstand washdown using high-pressure hoses. A regular cleaning process for automated agricultural equipment can be crucial to maintain it, especially when potentially corrosive substances such as fertilisers or pesticides are involved. For equipment end-users, full motor sealing, removing the need to apply protective covers, also makes the cleaning process much faster. Kollmorgen’s AKMA servo motors have been specifically designed for agricultural environments and, as a result, ensure a very high level of durability and protection.
Unlike most servo motors for industrial settings, which are based on a rectangular design, servo motors for outdoor use preferably feature a cylindrical body. This design enables liquid run off and prevents pooling. Kollmorgen can also achieve a vented design with a one-piece housing structure that eliminates the O-ring surrounding the motor shaft, a potential point of vulnerability for liquid ingress. The exterior of the motor should also be manufactured from corrosion resistant, highly durable material. Stainless steel is ideal, or anodised aluminium, and a coating that is resistant to scrapes helps prevent deterioration compared to a conventional epoxy.
Protecting the motor’s connections to the servo drive is also key. A single cable connection minimises vulnerabilities, and a stainless steel connector with a Viton seal, which is resistant to chemicals, extreme temperatures, and oxidation, should also be used.
Specifying a servo system
Delivering precision motion control for projects in arduous settings, INMOCO’s engineering team provides servo systems, including controllers, specific to application requirements. This involves system sizing, as well as optimising design integration and control architecture. For outdoor environments, including agricultural settings, this also means ensuring the right levels of durability and protection to achieve years of trouble-free use.
The advantages of smart farming haven’t yet been fully embraced across the UK. However, a new age, involving automated systems and machinery including agricultural robots, is set to make farming more productive, efficient, and sustainable. Servo systems will power many of these applications, and the importance of accurate specification, marrying precision control with durability, will be vital to this coming era.
Sources:
1) https://www.statista.com/outlook/tmo/robotics/service-robotics/commercial-service-robotics/agriculture-service-robotics/united-kingdom
2) https://www.statista.com/outlook/tmo/robotics/service-robotics/commercial-service-robotics/agriculture-service-robotics/united-kingdom