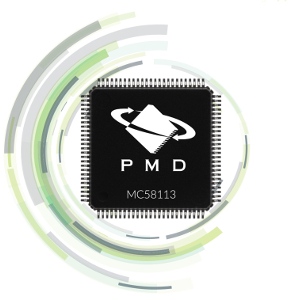
Off-the-shelf motion control chips or integrated circuits (ICs) are highly flexible and can in fact be used to control many other types of system, as Gerard Bush of INMOCO illustrates here.
Motion control systems rely on changing the speed of one or more motors in order to achieve a given outcome. For instance, glue laying and profile following typically use two motor driven linear actuators set perpendicular to one another. If you activate just one motor at a constant speed, the result is a straight line movement in one direction. Activate both motors at the same speed and you get a diagonal straight line. Activate them both but keep changing their relative speed and you get a curving line that may be required for laying glue around the periphery of a large vinyl letter prior to mounting on a board to make a sign.
The glue laying curve is analog, that is to say it varies steadily rather than stepping from one discrete point or ‘value’ to the next. However, most modern motion control systems are based on digital controllers not analog ones and approximate curves by moving in small steps between set point values. This arrangement works well, and indeed is the foundation of most curve following motion control systems in use today.
The same principle of curve following, using a series of small discrete steps, can be applied to many other analog systems including pressure and temperature control. To understand how this may work we can look at an example in which a standard IC is used to control the pressure of a reaction chamber.
High accuracy pressure control is a common requirement for many physical processes in biochemical, semiconductor and process control industries. OEM machine designers need an off-the-shelf and cost-effective solution for both single and multiple chamber vessels that provides accurate PID (proportional, integral, derivative) control and flexible pressure control profiles. This can be achieved using a Magellan® PID controller IC, as available in the UK through INMOCO.
The Magellan® family of ICs is best known for providing high performance chip-based motion control. They are available in 1, 2, 3, and 4-axis versions and can be used with different types of motors (settable by the user’s software), including brushed, brushless DC, and stepper, and in systems as diverse as profile following, pick and place, robotic arms, laboratory and medical equipment. They are designed for demanding and precise applications and are equally at home on non-motion applications such pressure valve control and temperature monitoring.
The basic principle for pressure control of a reaction chamber is based on a linear pressure sensor that outputs an analog voltage, signal conditioning, an analog-to-digital conversion (A/D) circuit, a Magellan® PID controller IC, output signal conditioning and a voltage-controlled flow valve. A host PC or microprocessor is also needed to communicate to the PID controller IC and provide overall sequencing and control of the reaction chamber or chambers. The IC, rather than its usual duty of motor control, provides the pressure control profile generation and PID pressure control.
In a pressure control system, the IC receives a parallel-word input from the analog voltage after it is converted to a digital signal. Its output mode is used to create a command voltage to the valve using an SPI-input drive chip. (SPI or Serial Peripheral Interface bus is a synchronous serial communication interface used for short distance communication, primarily in embedded systems.)
It is possible to use several different types of valve control signals, such as 4-20mA and +/- 10V DC signals, the choice of which will dictate the SPI drive chip to be used.
The Magellan® IC’s flexible architecture can be used to set a desired pressure, create pressure profiles with linear or parabolic ramps and/or set breakpoint conditions such as ‘automatically change to a new target profile after a specified pressure set point is reached’.
The PID sample/output rate is adjustable and needs to be tuned to meet the needs of individual systems. For typical pressure controllers, this means setting the PID loop sample time to between 10msec and 1sec.
The Magellan® IC can also be used to control temperature. In fact, it is common to control both pressure and temperature in a single reaction chamber. This would take up two ‘motion axes’ of the Magellan® control IC. The principle of control is the same; the input sensor provides a real-time temperature reading and the output from the PID drives a heater/cooler. Further, in multi-chamber reaction vessels, ‘two axis’ control in each chamber is needed to provide temperature and pressure for the full system.
The Magellan® range of ICs offers solutions to many different requirements. For instance, the MC58113 is a single axis IC with an integral digital current loop and amplifier switch signal generation. It can provide positioning, velocity, and torque control of motors but is equally at home on other duties such as pressure and temperature control.
Thus we have seen that motion control ICs are in fact very flexible and can be used in a wide range of other control applications. The analog input signals normally relating to acceleration and deceleration speed changes can in reality be representative of many other process parameters. This flexibility of use has many advantages such as reduced parts holding and designers being able to use chips with which they are already familiar.