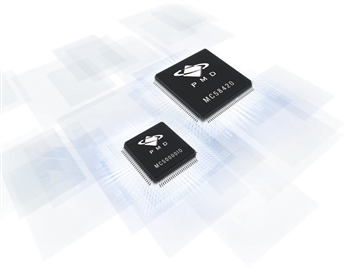
Inmoco has announced an optional ‘user-defined profile mode’ feature on Magellan Motion Control ICs (integrated circuits or silicon chips), which provides the capability for multi-axis synchronised continuous path profile generation on the chip.
Made by Performance Motion Devices in the United States, the chips are designed for use in dedicated motion controllers, rather than programmable servo drives. As such, they are ideal for applications such as 2D and 3D printing, robot control such as SCARA arms, biological and medical laboratory testing, glue laying, laser cutting and military equipment.
Flexible Multi-Axis Profile Generation
The user-defined profile mode is a flexible system for reading a stream of incoming positions or time values and using them to generate a corresponding continuous stream of commanded output positions. Because the relationship between the incoming data stream and the output positions can be entirely flexible, any desired shape can be drawn.
Master Axis Source Options
The user-defined profile mode allows one of three master axis sources to be selected: actual position from an external encoder; commanded position from an internal profile, or time. The choice of source determines the speed, whether the contour is synchronised to an external or internal source, and whether the contour is always traversed forwards or may also be traversed backwards.
When ‘actual position’ is used as the source, an external encoder is used, and the speed and direction are entirely controlled by it. This provides a cam function, where execution of the internal user-defined profile is synchronised to an external mechanism or other electronic signal source.
With the master axis source set to ‘commanded position’, one of Magellan’s internal axes provides the position data stream that is used to traverse the user-defined contour. This provides velocity control.
If the master axis source is set to time, the internal clock provides the incoming data. This means that neither the rate nor the direction of profile traversal will change, and that all available axes can be used to drive motors.
Settable Parameters for Profile Mapping
There are six settable parameters:
- Master Source selects the source of the incoming position or time data stream.
- Master Axis number selects the axis number of the incoming signal.
- Rate Scalar allows the incoming master source data stream to be accelerated, slowed down or reversed.
- Start Position and start index set where the profile will begin.
- Stop Position specifies the finish position or time
- IBufferID and PBufferID specify the memories that hold the incoming and output position data.
Once set, these parameters describe a particular mapping from the incoming data from the master axis to the driven axis commanded output positions. This mapping approach to profile generation forms the core of the user-defined profile mode, ensuring that synchronisation to the incoming data stream is automatic. Thus, if the incoming data slows down or speeds up, the output matches the speed change exactly, making it suitable for use in a wide variety of real-world applications.