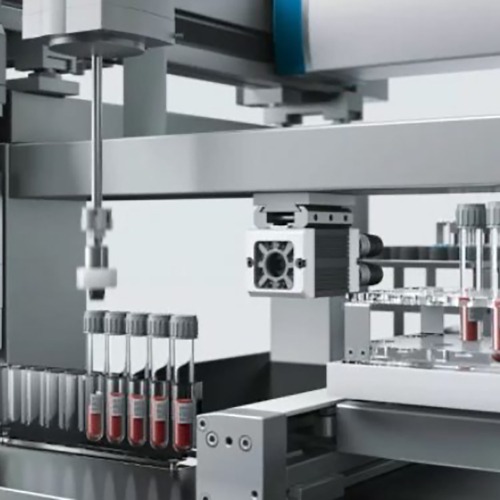
Understanding Gantry-Based Motion Control
In machine automation, gantry control is required across a range of applications, from 3D printing to CNC machining. As precision is crucial, this places high dependence on the gantry’s motion control system. Focussing primarily on design needs for compact machines and embedded control, there is a particular need to look at the motion control profiles and features required.
Gerard Bush, engineer at motion specialist INMOCO, discusses motion system specification for gantry-based applications.
Involving the management of a mechanism that moves along X, Y, and Z axes, a gantry can be used to navigate a tool or platform through three-dimensional space with a high degree of precision. Whether controlling a pipette on a liquid handling system, or a suction cup on a pick-and-place application, these machines rely on a gantry.
Operating to pre-programmed profiles, the gantry relies on a motion controller to coordinate three axes of travel. Each axis typically involves a motor with a sensor for position feedback, controlled locally by a drive.
Selecting Embedded Motion System Components
Motor control technology selection is highly dependent on the torque and control precision required by the application. For larger machine applications, AC servo motors are frequently used, with rotary motion converted into linear motion with belts, pulleys, or lead screws.
For smaller machines, typically requiring up to around 500W, brushless DC (BLDC) motors are increasingly integrated to optimise control precision, and linear BLDC designs can also be used. This technology also enables high-speed operation, required, for example, to maximise throughput on a pick-and-place application, rapidly accelerating and decelerating without losing position.
Also, for smaller scale applications, stepper motors are an alternative, ensuring repeatable accuracy by providing discrete ‘steps’ of motion. Traditional DC motors could also be integrated if cost is critical.
Motion Profiles for Precision Control
For applications where precision is vital, such as laser cutting or 3D printing machines, the control system must support smooth and accurate motion. Crucial to achieving this are the motion profiles of each axis, including the acceleration and deceleration ramps, commanded by the drives.
A typical requirement for gantry control is S-curve profiling, which adds stability as well as reducing mechanical stress. Shaped like the letter of its namesake, usually with seven individual segments of speed profile, the S-curve achieves smooth acceleration and deceleration.
The initial motion phase includes gradual acceleration to a set rate, where it then maintains a constant speed, before gradually decelerating. These controlled changes in speed reduces jerks, oscillations, and sudden stops, which enhances the smoothness of motion.
Techniques for Accuracy and Error Reduction
Another important technique is acceleration feedforward. Inertia can cause delays or position errors if left unmanaged, resulting in oscillations or overshoot, impacting accuracy and smoothness of motion. Acceleration feedforward mitigates these challenges by improving the system’s response.
To achieve this, the drive sends an additional command to the motor based on the expected acceleration, and this input enables the motor to achieve the desired acceleration from the outset. As a result, this technique reduces lag and ensures that the end effector reaches the target position accurately and smoothly.
Motion error detection is also important to ensure accuracy by identifying, in real time, unwanted deviations in the motion path or profile, and enabling corrective action. Vibration, for example, is a common challenge, which could cause motion path deviation sufficient to impact the precision. Combined with a feedback device that monitors deviation, a suitably intelligent drive can correct the error.
Design Integration and Specialist Support
When specifying a gantry control system, wider considerations are also required, such as needs in reliability, addressing thermal management and the demands placed on the system. Fundamental considerations on design integration, such as power supply, form factor, and installation, are also important, particularly for machines that require embedded electronics.
As a result of the complexity faced when developing a 3D gantry system, it’s often useful to engage with a specialist, like INMOCO. Dedicated motion engineers can specify the most suitable system for the particular requirements, and partner with motion vendors like Performance Motion Devices that offers a range of motion control chips and boards, as well as digital drives and modules for embedded designs. Engaging early with a motion specialist not only saves time in development, but ultimately helps to optimise the performance of the application.